It is extremely important to choose chemical cleaners carefully for their use, application, handling, and storage. In addition to the surfaces being cleaned, safety concerns include the general public, the cleaners, and the building or home in question. In the past, and even in some places now, cleaning chemicals have been mixed carelessly, which has caused serious harm to the surfaces and occasionally fatal repercussions for individuals concerned. Considering the wide variety of potent and unstable cleaning agents that are readily available, these activities are extremely dangerous.
The handling and storage of cleaning chemicals are commonly disregarded or given insufficient attention in the cleaning industry during safety audits and evaluations. There can be severe repercussions as a result. To ensure a safe workplace, it is crucial to handle and store these products properly. You can preserve efficiency and protect your employees by doing routine inspections once a year. You can ensure that your facility is secure and immaculate by following a few simple procedures.
What are cleaning chemicals?
Laundry detergents, bleaches, dishwashing detergents, and other household cleansers all contain chemicals that can aid increase cleaning effectiveness and cleanliness in homes, businesses, and other settings.
Cleaning solutions with chlorine help prevent the flu and foodborne illnesses, antibacterial cleansers help kill germs, and cleaning solvents, which generally have strong biodegradability, assist dissolve fats and oils.
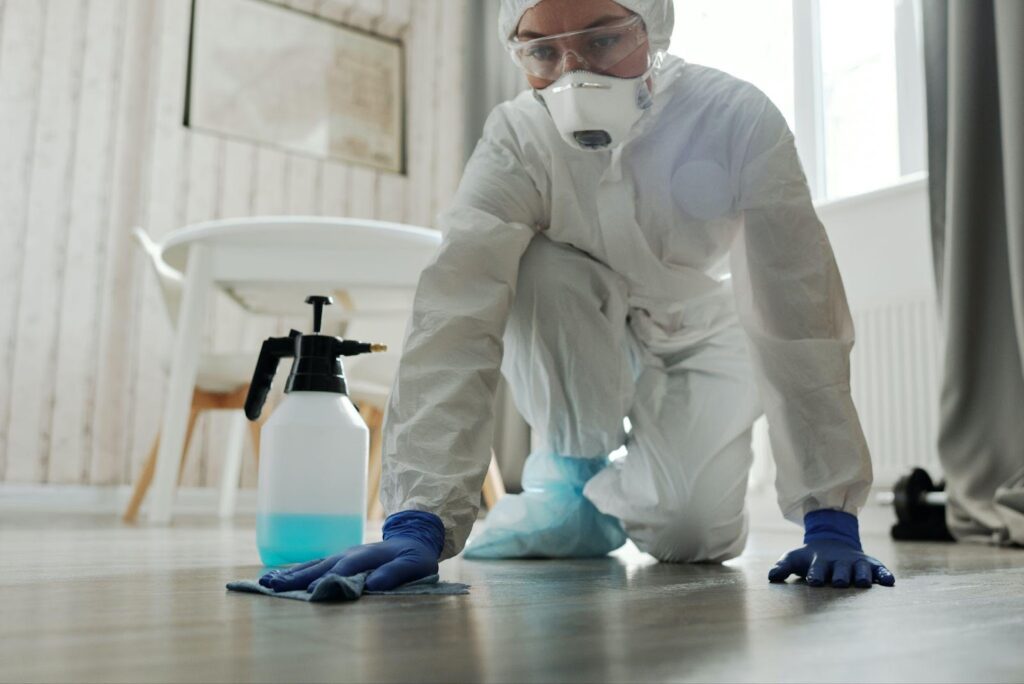
Clean and store cleaning chemicals safely
Both conventional and ecologically friendly cleaning chemicals can be safe to use when used properly. Yet, mishaps can still happen, therefore it’s critical to use caution when handling cleaning agents.
Due to the numerous chemical-related incidents that happen every year, the U.S. Department of Labor has ranked cleaning and custodial work as one of the most dangerous professions in the nation.
A successful chemical safety program is essential
Strict adherence to a chemical safety protocol is essential to ensuring the proper handling and storage of cleaning chemicals.
Here are some essential components that your chemical safety program ought to have:
- A detailed list of all cleaning agents used in the facility.
- Every cleaning product should include a Safety Data Sheet (SDS) that lists all potential risks associated with it.
- Designated cleaning supplies.
- Staff that has access to the necessary training materials and is adequately trained.
- Well-marked safety signage across your building.
Instruction in cleaning chemical safety for your employees
Just as important as providing your workers with the essential documentation is training them properly on how to use and store cleaning products. Several cleaning agents can be highly caustic or combustible, endangering the user. Employees may mistake high-risk substances for low-risk ones, which can have dangerous results.
To avoid this, it’s critical to inform all staff members about the following “signal words” and where to look for them on containers:
- Although it should be used with caution, the product is generally safe.
- The substance is mildly poisonous, so beware.
- The product is dangerous since it is extremely poisonous and can permanently damage the skin and eyes.
Picking the right place for cleaning chemicals
A thorough chemical safety program must include proper cleaning chemical storage as a key element. Even if the cleaning chemicals are used properly, disregarding storage guidelines can have dangerous effects.
To protect your team and the space, abide by these rules:
- Put cleaning supplies in a spot that’s clean, cold, and dry. It is crucial to remember that some cleaning agents might react chemically dangerously when exposed to excessive humidity or harsh temperatures.
- Put cleaning agents away from HVAC intake vents in a well-ventilated area. This makes sure that dangerous fumes don’t permeate your building.
- Never store cleaning agents on the top shelf; keep them at eye level or lower. Lack of anti-roll lips and crowded shelves might cause containers to fall, causing injury or property damage.
- Never, not even momentarily, keep cleaning agents on the floor.
Read More: How to Write SEO-Friendly Product Descriptions that Increase Sales
Managing cleaning agents for maximum safety
It’s crucial to arrange cleaning agents correctly within their assigned storage areas to maintain effectiveness and avoid mishaps. Chemicals must be separated according to their level of hazard, and it’s important to know which ones could react dangerously if mixed. As they respond to climate similarly, it is also advised to group products that are comparable together.
Substances that are oxidizers, flammable, or combustible should be kept out of the reach of anything that could spark an ignition, including flames, heat, sunlight, and in certain cases even static electricity. Flammable substances should be kept in an authorized, designated storage cabinet or room if the volume is greater than ten gallons. OSHA encourages following the National Fire Protection Association’s NFPA 30 standard for flammable and combustible liquids to ensure optimal safety.
Maintaining storage spaces and handling cleaning chemicals
To ensure proper cleaning chemical storage, it is essential to handle cleaning agents with care and uphold safety requirements. All containers must be kept sealed and kept in their original containers or containers that are suitable for the hazard class to which they belong. Even if two chemicals are of the same type, they should never be mixed. While not in use, portable cleaning product containers should be put back where they came from.
All product dates should also be known, and any outdated or unused items should be properly disposed of. Any product that has been open for more than a year or that has been sealed for more than two years should be thrown away. You can remove hazards and guarantee safety in your operations by adhering to the necessary documentation, training, location, organization, handling, and maintenance guidelines for cleaning chemical storage.
Final words
To guarantee workplace safety, chemicals must be stored properly. The containers for the chemicals should be labeled and well-closed, and they should be kept in a neat and dry environment. If a container leaks, it needs to be changed every away, and spills need to be cleaned up right away.
Never leave a container underneath a drum with the tap open since doing so can cause the contents to leak out, which is quite dangerous, especially when working with highly caustic or volatile chemicals. To avoid accidents and provide a safe workplace, it is critical to be on guard and implement the appropriate safety measures.
Author’s Bio:
Sally brings 26 years of experience to Warsaw Chemical. She began in Sales, managing customer training seminars. Later, she moved to Content Writing, crafting tech sheets for Warsaw Chemical and its customers.